les polymeres
Achetez Smooth-On chez FormX
Smooth-On est l'un des principaux fabricants mondiaux de matériaux de modélisation 3D tels que les matériaux de fabrication de moules, de coulée et d'effets spéciaux, mais aussi les résines de coulée industrielles, les adhésifs et les équipements. FormX est le principal distributeur des produits Smooth-On en Europe.
Forton et Duo Matrix
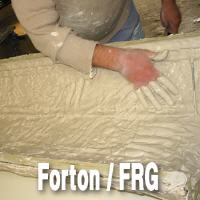
Des polymères qui permettent de réaliser des pièces en plâtre d'extérieur, résistantes aux intempéries.
Sécurité - Conserver et utiliser à température ambiante 23°C. Ces produits ont une durée de conservation limitée et doivent être utilisés dès que possible. Des températures plus froides ralentiront le temps de travail/durcissement, tandis que des températures plus chaudes réduiront les temps de travail. Les composants individuels doivent être stockés dans un environnement sec à température ambiante. Des conditions humides entraîneront une perte d'efficacité du plâtre et de la résine. Ne laissez pas le latex (C1) geler. Portez des lunettes de sécurité, des manches longues et des gants en caoutchouc pour minimiser les risques de contamination.
Préparation du moule - Si vous coulez dans un moule en caoutchouc uréthane, appliquez d'abord un agent de démoulage tel que Universal™ Mold Release ou Ease Release™ 200. Si vous utilisez un moule en caoutchouc silicone (Mold Max™ Silicone), le caoutchouc ne nécessite aucune préparation préalable.
Matériel requis - Assemblez tous les composants et accessoires avant de commencer. Tu auras besoin de:
- Conteneurs de mesure Alpha Gypsum
- Récipients de mélange de latex C-1
- Balance de pesée en résine C-2 (balance numérique à gramme ou à triple faisceau)
- C-3 Hardener Mechanical / Power Mixer (Jiffy ou Squirrel Mixer)
- Masque anti-poussière approuvé NIOSH
- Écran de fenêtre ou similaire pour filtrer le mélange
Composants Matrix - Le système de base Matrix™-G se compose de 3 composants (C1 + C2 + C3) qui sont mélangés avec un gypse alpha.
Composant 1 (C-1) Latex : Un liquide blanc qui agit comme un liant et confère au dMG des propriétés de résistance à l'eau.
Composant 2 (C-2) Résine : Fine poudre blanche qui réagit avec le composant 3 et le gypse. Améliore les propriétés physiques du mélange global.
Composant 3 (C-3) Durcisseur : Poudre cristalline - ressemble à du sucre. Différents niveaux affecteront le temps de travail/démoulage.
Alpha Gypsum : Vous ne pouvez pas utiliser n'importe quel produit de gypse/plâtre. Vous devez utiliser un Alpha Gypsum tel que FGR 95 de USG Corp., Densite HL de Georgia Pacific, Crystacal R de British Gypsum ou équivalent.
Important : N'utilisez que des matériaux frais… les anciens matériaux (plâtre, latex) donneront des résultats incohérents.
Parce qu'il n'y a pas deux applications identiques, une petite application de test pour déterminer l'adéquation à votre projet est recommandée si les performances de ce matériau sont en cause.
Mesure et mélange - Pour minimiser l'inhalation de poussière, nous vous recommandons de porter un masque anti-poussière approuvé par le NIOSH lors de la pesée et du mélange des composants. Une balance précise (échelle en grammes ou balance à triple faisceau) est nécessaire pour réussir avec ce produit. N'utilisez pas de pèse-personne, de diététique ou de salle de bain pour peser les composants.
Important : Les composants doivent être mélangés dans le bon ordre. Un mélangeur électrique doit être utilisé pour mélanger tous les composants.
Étape 1 : Bien agiter ou remuer le latex C-1 et verser la quantité requise dans le récipient de mélange.
Étape 2 : Combinez tous les ingrédients secs : combinez le gypse + la résine C-2 + le durcisseur C-3 en poids dans un récipient de mélange de taille appropriée (si vous ajoutez des charges telles que du verre haché, de la poudre de bronze, des pigments secs, etc., mélangez avec des composants secs avant d'ajouter du latex C-1). Bien mélanger les composants secs à l'aide d'une palette de mélange, d'un mélangeur électrique, etc. jusqu'à ce qu'ils soient bien mélangés.
Étape 3 : Tamiser le contenu de la poudre dans le latex C-1 et mélanger tous les composants avec un mélangeur électrique jusqu'à ce que tous les composants de la poudre sèche soient complètement dispersés (minimum 90 secondes).
Les quantités de composants varient en fonction de la taille du lot que vous fabriquez.
Accélération de Matrix™-G - Matrix™-G Accelerator (poudre) réduira le temps de démoulage de Matrix™-G et doit être pré-mélangé avec des composants secs avant d'ajouter du latex. Remarque : Plus le temps de démoulage souhaité est court, plus le temps de travail est court.
Slowing Matrix™-G : certaines applications peuvent exiger qu'une grande quantité soit mélangée et coulée dans un seul moule (moulage en masse) ou pour un "mélange maître" (une grande quantité est mélangée et versée dans de nombreux moules différents pour la coulée de production). La réduction du durcisseur Matrix™-G (C-3) donnera un temps de travail et un temps de démoulage plus longs.
Coulage et application - Après avoir soigneusement mélangé les composants, le mélange est prêt à être versé dans un moule. Pour les meilleurs résultats:
1. Appliquez une couche de face de Matrix™ sur la surface du moule. Cela aide à briser la tension superficielle et finalement à réduire les bulles d'air.
2. Après l'application d'une couche de finition, le mélange restant est lentement versé à travers un écran de fenêtre, une passoire de cuisine ou équivalent dans le moule. Cela aidera à éliminer tout produit non mélangé et contribuera à réduire davantage l'air emprisonné.
Réduction supplémentaire de l'air emprisonné - Les bulles d'air sont parfois un problème avec les gypses modifiés aux polymères et varient en fonction des conditions. Il existe des mesures supplémentaires que vous pouvez prendre pour aider à réduire l'air emprisonné : 1. Vibration – les couleurs de béton font souvent vibrer leurs mélanges de béton sur une table vibrante pour réduire l'air emprisonné. En faisant vibrer le moule, l'air va monter et se dissiper à la surface. 2. Pression – Obligatoire : Récipient sous pression et compresseur. Une fois le mélange versé dans le moule, placer le moule dans un récipient sous pression et soumettre le mélange à une pression d'air de 60 PSI (4,2 kg/cm2) pendant une heure. La coulée sous pression est le seul moyen d'éliminer complètement les bulles de votre mélange. L'aspiration du matériel ne fonctionne pas.